Cyanotypes
and Digital Negatives by Christopher John Ball
The
invention of the Cyanotype process is accredited to Sir John Herschel,
the Astronomer Royal, in 1842. It is believed that he developed
this process so as to be able to make accurate copies of his designs,
calculations and notes. Artists were initially employed to copy
the designs by hand but Herschel became dissatisfied with the mistakes
and the resultant inaccuracies that arose and so the 'Blue-print'
came into being.
It
did not take long for the process to be exploited by photographers
after it was found that it could be used to produce prints from
continuous tone negatives, provided that they exhibited plenty of
contrast.
The
Cyanotype is a printing out process using an ultra violet light source.
It is one of the oldest and most permanent printing processes still
in use by Fine Arts Photographers and it is the simplest ‘alternative’
photographic process to undertake.
Nude
studies are excellent subjects for making cyanotypes. The brush strokes
in the coating process produce edges that give a unique look to each
print and the surface texture of the water colour paper becomes part
of the final image to create a subtle aesthetic. Cyanotype image making
is a fun process that affords the photographer of the nude a creative
outlet that combines the digital technologies with historical processes
to produce unique photographs with a hand made organic look.
Cyanotypes
are produced by contact printing a negative therefore the final image
is the same size as the negative. This meant that to produce a print
of a decent size required a large format camera.
The
arrival of quality inkjet printers has removed that necessity. The
photographer can now shoot on any film or digital medium and then
produce a negative via inkjet means to the required size.
Making
the Digital Negative:
I
favour making negatives via an inkjet printer and printing out to
the desired size onto Overhead Projection Film
.
Inkjet negatives give the photographer greater control over the finished
image. You are free to make whatever alterations to the negative (dodging,
burning, cloning, cropping, convert colour images etc) that you wish
in the image manipulation software of your choice.
Pictorico
transparency film is recommended by many practitioners as it has a
gelatine and ceramic coating which has superior ink holding properties
to standard OHP material, but feel free to experiment with other manufacturers
as this isn't as widely available as it used to be. Look for a good
quality overhead transparency film from a respected manufacturer.
Select
the image that you wish to make a negative and go to Image>Adjust>De-saturate.
Next you need to turn the image into a negative. Do this by going
to Image>Adjust>Invert. To alter contrast go to Image>Adjust>Levels.
In levels adjust the Output with the bottom sliders from 0 to 255
to about 20 to 210 (fig 1). This is a starting point
and you may find that, after experimentation, other settings suit
your images better.
You
could print the negative at this stage but I recommend filling the
image with another colour. Rather like the orange mask used in colour
film negatives - using your software’s fill command. This allows
for a denser negative as the additional colour adds ink.
From
the Toolbox select the foreground colour icon. The colour picker box
will open. In the C.M.Y.K % section change the settings to C=0, M=50,
Y=50, K=0 (fig 2). This will produce an orange colour
in the Foreground Box similar to the orange cast found in colour negative
film. Click OK. Now go to Edit>Fill. Select OK (fig 3).
The image will turn completely orange (fig 4). Next
go to Edit>Fade Fill. A dialogue box will open. With the Mode setting
left at Normal – slide the Opacity slider until it reaches 40%
(fig 5). Click OK. You may want to experiment with
the percentage but 40% is a good starting point. Save your work.
The
final stage is to flip the negative image horizontally (fig
6) – if you fail to do this your image will appear
as if in a mirror.
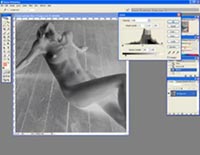 |
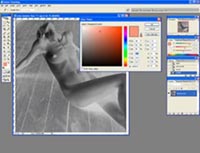 |
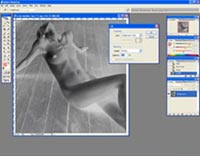 |
fig
1 |
fig
2 |
fig
3 |
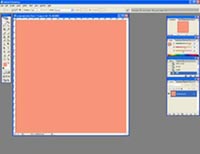 |
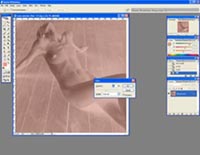 |
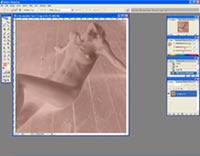 |
fig
4 |
fig
5 |
fig
6 |
Finally
print, at your printer’s highest resolution onto your OHP transparency.
Handle the negative carefully by the edges and hang it up to dry and
harden away from dust.
Paper:
Whilst practically any paper can be used to make a cyanotype print
most photographers favour using a quality acid free watercolour paper
of about 300gms in weight. The beauty of the cyanotype process is
that you can experiment with differing paper surfaces and tones -
try an off-white/cream or ivory paper.
Lighting
Source: Traditionally the sun was used as the light source but an
artificial UV source may prove to be more controllable. I uses a small
facial sauna. This 'mini-sunbed' has the dual advantage of being a
constant source of UV and of having a built in timer. This allows
for more accurate and repeatable exposures.
Printing
Frame: A rim-less clip frame, of the sort used to display posters,
can be modified for use as a cyanotype printing frame. Cut the backboard
of the clip frame in two about half way and tape these two parts back
together with heavy-duty tape to form a 'hinged' back. The frame can
be opened as normal to load your paper and negative, and then clipped
back together, using 4 large ‘bull-dog’ clips, to hold
the two in register while you make your exposure. To check the progress
of the print, simply remove 2 clips from the top half and 'open' the
hinged back. The remaining clips ensure that the negative and paper
stay in register.
Materials
1- Digital Scale with at least 0.5 g. of accuracy.
2- Two brown medicine bottles of at least 150 cc each. To hold solutions
A and B
3- Rubber or latex gloves.
4- 250cc glass beaker.
5- Japanese calligraphy brushes (Hake – brush without metallic
ring)
6- UV light source or sun.
7- Contact printing frame.
8- Developing trays larger than the size of the sensitised paper being
used.
9- Water Colour Paper – Acid free 300gms
10- 500ml measuring cylinder
11- Plastic clothes pegs to hang paper to dry.
12- OHP transparency on which to print the negative.
Cyanotype
Formula
Formula OneSolution
A 20 grams Ferric Ammonium Citrate (green) + 100ml water at 22C.Solution
B 10 grams Potassium Ferricyanide + 100ml water at 22CTo
Use: mix equal parts of A and B. Has limited shelf life when mixed
Formula TwoSolution
A 20 grams Ferric Ammonium Citrate (green) + 5 grams Oxalic Acid (HIGHLY
TOXIC) + 100ml Water at 22CSolution
B 10 grams Potassium Ferricyanide + 5 grams Oxalic Acid (HIGHLY TOXIC)
+ 2 grams Ammonium Dichromate + 100ml Water at 22C.
To
Use: mix equal parts of A and B. Has limited shelf life when mixed
Procedure
1.
Mix equal parts of ‘A’ solution and ‘B’ solution.
The chemicals become sensitive when mixed together. Stored separately
the chemicals keep well but once mixed the solution must be discarded
after 24 hours – so mix only what you need at the time. Sensitised
paper also does not keep well overnight so it is best to coat the
paper as needed.
2.
Under subdued light apply the solution with a brush – some practitioners
prefer to coat the paper using a glass rod but I prefer the look that
brush coating gives to the edges of the image. It is important that
you use a stitched brush, i.e. one whose bristles are not held in
place by metal crimping. The metal can react with the solutions giving
adverse effects. Japanese calligraphy brushes (Hake) are ideal. Use
smooth, even strokes of the brush again in the opposite direction.
3.
Let the coated material air dry in total darkness. Do not use heat
to dry the paper as it may cause fogging. The coating should dry to
a bright yellow.
4:
Place the dry paper emulsion-side up and the negative emulsion/ink-side
down in the contact printing frame.
Caution:
potassium ferricyanide bleaches silver so if the paper surface is
not dry, the negative will be destroyed.
5.
Expose the coated material for the desired time, handling it with
care. Time will vary due to the light source used and the density
of the negative but I suggest 20 minutes as a starting point before
checking the image. Exposures can take as long as an hour so patience
is called for.
6.
Developing/Washing/Fixing: After the exposure is completed the print
is ‘developed’ in running water, at approximately 68°F
(20°C), for about 20 minutes or until the yellow stain disappears.
This will clear the highlights. Sometimes the print may look a little
dark with the highlights looking degraded and a little muddy. Though
it is often best to make a new print, and simply adjust exposure time,
mild cases can be corrected by adding two table spoons of distilled
clear table vinegar to a litre of water and applying this solution
to the wet print to clear the highlights.
7.
Intensifier: After the print has been developed it can be treated
in a solution of a few drops of Hydrogen Peroxide in 500ml of water.
This solution acts as an intensifier and will enrich the cyan colour.
Leave the print in the solution for a couple of minutes but do not
increase the time because the image will begin to fade. Wash the treated
print in running water for 15 minutes and hang to dry.
8.
Allow the print to air dry in subdued light.
Toning/Staining Cyanotype Prints
Cyanotypes
can be toned to produce several different colours. Unfortunately the
process of doing so can be a very hit or miss affair. Do not let this
put you off as, with a little patience, experimentation and luck,
the results can be well worth the time and trouble involved.
N.B.:
If your are going to tone prints that you have previously produced
and dried, before toning, soak the prints, briefly, in distilled water
at room temperature.
Green
Make
a saturated, 20ml, solution of Iron (II) Sulfate. Add to this - 4
drops of Sulphuric Acid and then dilute with an equal amount of water
(20ml). You should now have 40ml of toner into which the print can
be immersed. Once the desired tone has been achieved remove the print
and wash in water.
Lilac-violet
Place
the print in a solution of borax and water. Wash after the desired
tone has been achieved.
Mauve,
Grey and Red
This
solution will produce all three tones. It's just a question of how
long you leave the print in the solution. There are no hard and fast
rules to the length of time as there are too many variables. Therefore
this has to be done by inspection and it does not always work, but
when it does the results can be beautiful. Print darker than usual
and then wash for 10 minutes, then immerse in a solution of Copper
Nitrate (into which a few drops of ammonia have been added - add drop
at a time until the precipitate has redissolved. This bath turns the
print first mauve, then grey and then finally red.
Black
Toner
Solution
A: 3 drops Nitric Acid + 1000 cc. distilled water
Solution
B: 14g. Sodium Carbonate + 160 ml. distilled water
Solution
C: 14gGallic Acid + 160 ml. distilled water
Soak
the print for 5 minutes in water. Immerse it in solution A for 2 minutes.
Wash the print in water for 5 minutes. Immerse the print in the solution
B and leave it until the image bleaches away and then reappears as
a light orange image. Wash the print for at least 10 minutes in water
and the place it in solution C. When the image has achieved the required
black tone remove and wash for at least 40 minutes in water. Finally
allow the print to air dry.
Reddish
Brown Highlights with Bluish Grey Shadows
Solution
A: 36 g. Tannic acid + 1000 cc. distilled water
Solution
B: 18 g. Sodium Carbonate + 1000 cc. distilled water
Solution
C: 30 cc. of a 3% Hydrogen Peroxide solution + 1000 cc. distilled
water.
Place
a presoaked cyanotype in solution A for 2 minutes. Wash for 2 minutes
water. The print is then immersed in solution B for no longer than
20 seconds. Remove the print and wash for 2 minutes in water. Now
place it in solution C until it gets the desired tone is reached.
Finally wash the print for at least 30 minutes in order to eliminate
any residual chemical from the print and let it air dry.
Staining
in Tea solution
The
tannic acid in tea is an excellent means of staining cyanotypes brown.
Simply prepare a concentrated tea solution (don’t use Earl Grey)
and leave the print immersed in this solution until the desired tone
is reached. Wash with plain water for 15 minutes and let it dry.
Caution
Whilst
the cyanotype process is relatively safe - like any photographic process
a few simple precautions are necessary and all chemicals should be
kept out of the way of children and it is important not to have food
or drink in the work areas.
Wear
rubber gloves. Cyanotype chemicals will stain the skin and clothing.
Do
not let these chemicals come in contact with your eyes. If they do,
flush eyes immediately with running water for at least 10 minutes
and contact your doctor immediately.
If
any of the chemicals are accidentally ingested get medical attention
immediately. The antidote for potassium ferricyanide is 3% hydrogen
peroxide in a dilute solution.
Always
clean everything after each session. Clean your hands thoroughly and
make sure that all bottles are labeled correctly.
Be
sure to prevent acid from coming into contact with any cyanide; such
a combination will produce poisonous cyanide gas.
July 2024 Several books, featuring Christopher John Ball's photographs, are now available through Amazon or click on an image below to purchase via secure payments on lulu.com